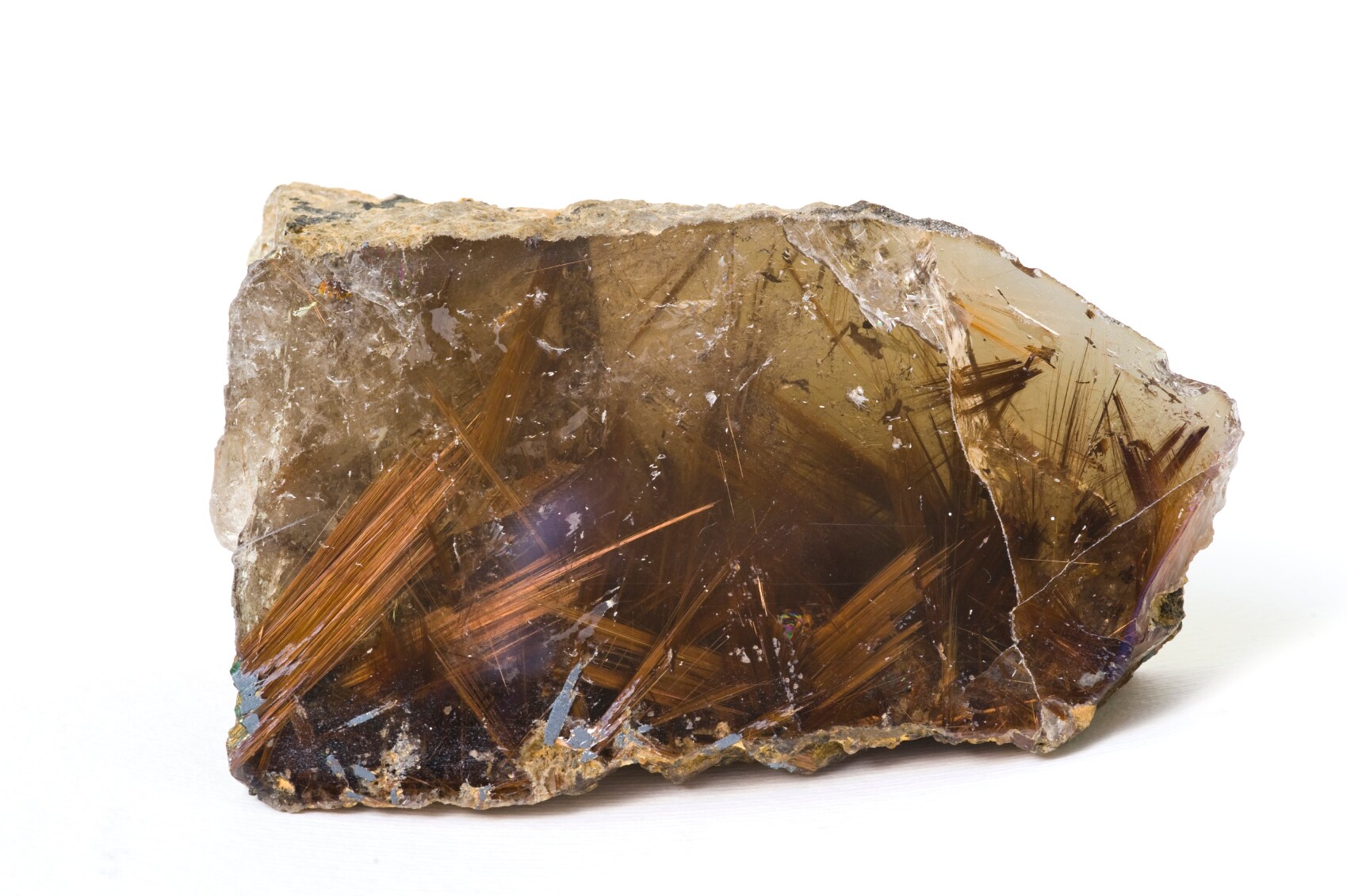
Rutilated quartz, shown here, is a rare mineral that is mainly made up of titanium dioxide (rutile) within quartz.
Discovered by William Gregor in 1791, titanium is a white metal when pure, and is the 9th most abundant element in the Earth’s crust. As a metal, titanium is well known for corrosion resistance and for its light weight but high strength-to-weight ratio. These are probably the reasons it can be found almost anywhere. (See Titanium: This Lightweight Does Some Heavy Lifting in the Metals Industry.)
The rise of additive manufacturing, or 3D printing as it’s commonly known, is only increasing the use of this versatile metal. 3D printing with metal was once cost-prohibitive, but now 3D printing technologies for metal may be more efficient than some traditional manufacturing methods and produce a comparable, or even better product, depending on the application. And titanium is getting in the game. See our Analyzing Metals article on New Research on 3D Printing with Titanium to learn how formulations of various grades of titanium and other alloys are being used in the evolving 3D printing industry. The article addresses a study conducted by Carnegie Mellon University and the Argonne National Laboratory that focused on Ti-6Al-4V powders printed by electron-beam melting (EBM).
Metal alloy composition, whether it’s being used in an additive or traditional manufacturing application, must be verified to ensure product chemistry specifications are met. Wavelength-dispersive x-ray fluorescence (WDXRF) is a nondestructive analytical method that quickly provides the exact percentages of a wide range of elements for material characterization and analysis.
Read the New Research on 3D Printing with Titanium article.
Leave a Reply